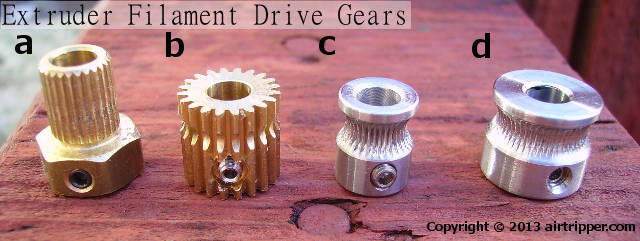
3D Printer Extruder Filament Drive Gears: a, Plain Insert; b, Raptor Filament Drive Gear; c, MK8 Drive Gear; d, MK7 Drive Gear
Probably the most important part of the 3d printer direct drive extruder system, at least after the stepper motor, is the filament drive gear pulley. Basically, the choice of drive gear could make or break the quality output of the 3d printer. Without a good drive gear, it will be difficult to begin to troubleshoot or solve hot end issues. So, with the help of the Airtripper Extruder Filament Force Sensor, I’ve reviewed and bench-marked four drive gears and provided graphs for a quick visual comparison.
All the benchmarking and the drive gear reviews in this topic are based on PLA filament only, softer filament might provide very different results, so a separate review would be needed for different filaments. Since PLA filament can be difficult to extrude, this was a good filament to do the first drive gear benchmark with.
It’s almost certain that some of the drive gears will perform much better on geared extruders, but for this topic, only direct drive extruder is used. I think the benchmark results for drive gears are more interesting when the torque limits of the stepper motor are also shown.
Filament Drive Gear Review & Benchmark
The Benchmark Testing Procedure
The benchmarking is done with the Sumpod 3d printer fitted with the Airtripper Extruder Filament Force Sensor; an introduction to the filament force sensor can be found here. Filament is extruded through the hot end nozzle in air away from the build platform. Enough filament is extruded until filament force has reached its peak, and then continue extruding to be sure that the drive gear can push against the force without filament slipping or stepper motor stalling.
Screen capture is used to capture the Processing application graph at the point of interest. The extruder flow rate is either increased or decreased depending on the drive gear performance. Flow rate is increased to cause the filament pushing force to rise to the point of failure, of either the stepper motor (stalling) or the drive gear (slipping). Adjustments are made to the extruder idler tension to try to compensate for failures and to fine tune for better performance.
Each drive gear pulley is calibrated for the correct value for E Steps/mm. A starting value is entered into the Marlin firmware before extruding 100mm of filament for measurement. 100mm of fresh filament is extruded from the printer interface with the driven filament length being measured for length accuracy. E Steps/mm is updated as necessary to satisfy calibration test accuracy before benchmarking.
Plain Insert Coupling
Brass, bore 5mm, length 15mm, effective diameter 7.66mm approx. E step calibration starting point for 1/8 micro stepping 67.16.
This gear was originally supplied with the MDF Sumpod; my first 3d printer. It’s usually called a Plain Insert Coupling, used for connecting universal joints to motor shafts in model boats. A quick google search “plain insert joint” found a number of suppliers with prices around GBP 2.00 (USD 2.64). Similar to the Plain Insert Couplings, a range are also sold under the brand Raboesch Couplings. The prices for the range are slightly more, GBP 2.26 (USD 2.97), and sold by Boots Industries as a drive gear for CAD 14.99; so shop around. Plain Insert Couplings and Raboesch Couplings look very similar but can’t tell how closely matched the teeth are without having both types in hand.
If the Plain Insert can seriously be used as an extruder filament drive gear then this would be the cheapest drive gear available by far, and graph one confirms that this gear has some pushing power. I can’t say that my experience with the Plain Insert has been good, I had a lot of other issues with the Sumpod extruder and with my inexperience at the time it would not be fair to judge the gear by past experience. So, my opinion of the Plain Insert Coupling will be derived from the benchmarking test.
The teeth are triangular shaped, slightly flattened on top, and angled at the bottom between each tooth; a design that will mostly prevent the gear teeth from fully penetrating the filament. So, because of the shape of the teeth, and as confirmed by the teeth marks on the filament, the effective diameter will be determined by the filament type and idler tension. It is likely that there will be flow rate differences between filament types and E step calibration.
Extra care needs to be taken to setup this drive gear, getting the correct tension on the filament, and checking the E steps/mm and flow rate. Over tightening the idler tension can have a negative effect on performance as shown in graph three, and this is due to the stepper motor torque being used to compress the filament between the teeth of the gear; making the extruder stepper motor work harder.
Graph one and graph two show that the extruder idler tension is optimized for best filament grip with graph two being influenced by increasing hot end flow rate to the point of stalling the extruder stepper motor. Graph three shows the extruder stepper motor stalling under increased idler tension.
Although the the Plain Insert as shown good performance for this benchmarking, achieving the same result will be difficult without an extruder filament force sensor. This gear does not have the same high level of grip as the MK7 and MK8 and so hitting the margin between filament slips and stepper motor stalls with idler tension tweaking will be more difficult at higher forces.
Raptor Filament Drive Gear
Brass, bore 5mm, length 11.2mm, effective diameter 9.67mm approx. E step calibration starting point for 1/8 micro stepping 49.7.
The Raptor Drive Gear was offered by QU-BD alongside their new MBE Extruder V9 at a time when 3d printer parts was much less available than they are today. During that time, filament drive gears for direct drive extruders was quit rare and expensive to import. So when the Raptor Drive Gear came to market with favorable shipping costs, I ordered two to replace the Plain Insert Coupling that I was then using. Unfortunately, my extruder woes didn’t end.
I’m not sure how the QU-BD company did the benchmark for this drive gear but I could not get it to work with PLA filament; so I’m assuming the performance claims was made against ABS filament. Even with the filament force sensor, I could not get a reliable flow rate above 2kg of force. Graph one shows the best force level I could achieve without filament slipping or stepper motor stalling.
With increased filament flow rate, graph two shows the filament slipping on the drive gear leading to under extrusion. When attempting to compensate for the slippage, graph three shows the result. The flattened teeth on the Raptor causes more work for the stepper motor as the teeth get pressed into the filament under increased idler pressure. The harder the teeth get pressed into the filament the less force is available to push the filament, eventually leading to stepper motor stalls.
The Raptor Drive Gear has deep teeth which may effect flow rate calibration accuracy between filament changes and E Step calibration. If the drive gear teeth don’t fully sink into the filament then the effective diameter of the drive gear might not be consistent between different filament types. This would complicate filament set-up and you would have to set-up the idler tension correctly as before when reinserting filament previously calibrated.
The grub screw was a problem for me while using this gear, the Raptor often come lose on the stepper shaft. Personally I thought the wrench required to fit the grub screw was too thin for the tightening toque needed, and sometimes it slipped round in the screw head. In the end, I manage to fined a grub screw with a larger hex socket to insert into the Raptor; which did the trick.
MK8 Filament Drive Gear
Machined stainless steel (304), bore 5mm, length 10.1mm, effective diameter 7mm. E step calibration starting point for 1/8 micro stepping 75.7.
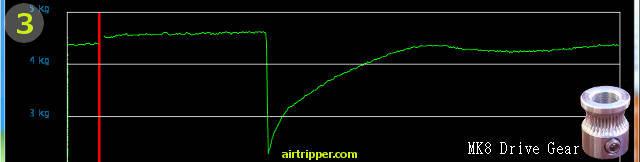
MK8 Dive Gear Stalling the stepper motor at over 4.6kg of force. Good filament grip is demonstrated here.
When I ordered the MK8 Drive Gear I had doubts about its ability to grip the filament with performance on par with that of the MK7. This was due to the reduced diameter, giving 35% more power as claimed, which I thought would compromise the effective grip on the filament. But it turns out that the MK8 Gear can maintain excellent grip on the filament right up to the point of stalling the stepper motor. It’s reduced diameter, compared with the MK7, makes better use of limited torque provided by 3d printer direct drive extruders.
The MK8 Drive Gear’s fine milled teeth allows the filament to be held against the effective diameter easily by the idler bearing; allowing for consistent flow rate calibration between filament changes and E Step calibration.
Graph one shows the level of force that can be achieved with the MK8 when the extruder idler preload is optimized. Achieving this level of set-up will be difficult without a filament force sensor and this is due to the filament slippage, shown in graph two, being difficult to detect. However, since this drive gear is capable of stalling the motor as shown in graph three, cranking up the feed rate fast enough to see if you can stall the stepper motor will indicate if the idler is tight enough to prevent filament slippage.
Even without a filament force sensor, for a well maintained 3d printer extruder system, this gear is easy enough to set-up without special considerations or set-up exercises; since the high level of forces achieved by this gear may never be needed for normal 3d printing conditions.
MK7 Filament Drive Gear
Machined stainless steel (304), bore 5mm, length 11.1mm, effective diameter 10.56mm. E step calibration starting point for 1/8 micro stepping 48.1.
Purchased from Ebay, the MK7 Drive Gear turned out to be the most important update to my 3d printer extruder system. After struggling with the Raptor Drive Gear for some time, with the MK7 fitted, I was now able to solve extruder issues rather than manage issues. My extruder suddenly became more reliable and I was now getting the correct feedback needed to calibrate settings to get the best looking 3d prints.
The MK7 with its large effective diameter provided excellent grip on the filament which meant less care about idler tension set-ups. Like the MK8, consistent flow rate calibration between filament changes and E Step calibration was possible due to the gears’ finely milled teeth. Also to note, the MK7 grub screw worked well and its hex socket took a decent size wrench to lock the gear on to the stepper motor shaft with plenty of torque.
Although the MK7 performs well in the grip department, its large effective diameter means there is less torque to drive filament through the hot end. Compare graph one to the MK8 Drive Gear and you’ll see a performance gap between two similar designed gears but with different effective diameters. Looking at graph two the MK7 stalls at around 3kg of filament force, probably not ideal for direct drive extruders but there is enough torque for a good hot end set-up. It’s only when you start having hot end issues that this gear will show it’s torque limitations, and that’s what prompted me to change to the MK8 Gear.
The MK7 Drive Gear would work better with geared extruders or even NEMA23 stepper motors. But options are limited while the MK7 is only available with 5mm bore, an 8mm bore version to fit Planetary gear stepper motors would be welcome.
Filament Drive Gear Review & Benchmark Conclusion
The drive gears may provide very different results for different types of filament, but for PLA filament at least, the MK8 Drive Gear came top in this article. I would recommend the MK8 Drive Gear for direct drive extruders, especially when paired with the stepper used for this test. The MK8 Drive Gear provides a good balance of grip and torque to push the filament with force that easily exceeds 4kg.
The MK7 Drive Gear would be my second recommendation, it has excellent grip on the filament and the idler tension is easy to set-up. However, the gears’ large effective diameter may not provide enough torque when nozzle and filament troubles occur. If you’re looking for serious pushing power from a geared stepper motor, the MK7 should be first choice.
The MK7 and the MK8 have been engineered for the purpose of extruding filament and have provided good all round performance; both easy to set-up with the extruder idler tension.
The Plain Insert Coupling deserves a mention for its good pushing power. However, the gear can be difficult to set-up without the help of the filament force sensor. If you have good experience with 3d printing and have a well oiled machine, you might get some good performance out of this cheap drive gear.
And finally, performing very poorly, the Raptor Drive Gear. As proved with the MK7 Drive Gear, bigger gear teeth don’t mean better grip. However, the Raptor Drive Gear might perform better on a geared extruder where idler tension can be increased, but at the expense of causing more damage to the filament.
[bodyadsrich1l]
Related Articles
Arduino Load Cell Circuit & Sketch for Calibration Test
Airtripper Extruder Filament Force Sensor – Introduction
Airtripper’s Bowden Extruder V3 – Updated Design
3D Printer Extruder Filament Drive Gear Review & Benchmark
A thorough and scientific review. In the Airtripper V3 extruder, the filament path looks like designed for 7-8mm effective diameter gear. When putting a MK7 (10mm effective diameter), the filament will not be a straight line but a little bended by the gear. I am wondering if this will affect the result of the measurement.
Myself using an Airtripper variation for planetary stepper with mk7 gear with 8mm bore (from ebay) and a 1:5 geared motor. I am pretty satisfied by the performance.
Thanks!
Hi Jason,
The filament does curve round the MK7 Drive Gear, but with it’s large difference in the effective diameter against the MK8 Drive Gear, a little extra filament friction is minimal compared to the already reduced torque of the stepper motor.
I did recommend using the MK7 Drive Gear on a planetary stepper motor later in the post, it’s larger diameter will then become an advantage because of it’s wider surface contact with the filament; I reckon you have the best gear for your geared stepper.
MK7 Drive Gear on direct drive extruders has worked reliably, it’s only when there is a problem with the hot end where the stepper motor starts to stall.
Mark