I’ve been using this heated build platform for a while now and so far been happy with it’s performance. However, for the larger prints and longer print runs, the base of some prints start to warp and become unstuck from the glass on the heated build platform leading to some prints not making it to the end of printing. To keep warping to a minimum, the first layer of the print needs to be stuck down well to the heated build platform. To achieve this, some investigation is needed so that a solution can be considered.
When testing the temperature of the heated build platform I found that when the heating element is powered, the temperature difference went as high as fourteen degrees C on the glass between the thermistor and heating element. I believe this temperature difference, which was happening about every 230 seconds, caused enough contraction and expansion to cause prints to become unstuck from the glass. Clicking and cracking sounds can be heard during printing as the print starts to become unstuck from the heated build platform.
Heated Build Platform Analysis & Rework
Analysis
Armed with a laser guided heat sensor gun, a stop watch and a spread sheet, I set about finding out what was going on. I preheated the glass bed and let it go through the heating cycle a few times before taking the measurements.
I pointed the heat sensor gun at the target and took measurements for the duration of a heating cycle. The targets for this exercise is the glass area above the nichrome wire and the glass area above the thermistor. See the chart below.
From the chart, when the heater is powered, the temperature on the glass above the nichrome wire climbs to 68 degrees C, 13 degrees C above the target temperature. It takes about 30 seconds for the thermistor to detect a temperature rise, and when the target temperature is reached, the nichrome wire heating element is powered off.
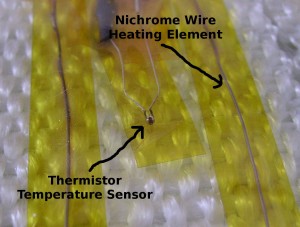
3D Printer Thermistor Close Up
While the nichrome heating element is powered off, the temperature in the glass above the thermistor continues to conduct heat from the hotter areas of the glass which lasts for around 50 seconds. During the next 140 seconds the temperature starts to drop gradually and becoming more evenly spread across the glass before the heating cycle starts over again.
Conclusion
The low thermal conductivity of the glass and the position of the thermistor being far from the heat source is causing uneven heating of the glass and poor heat control. Areas of the glass get far too hot, much higher than the target temperature. The target temperature is not maintained and only reliably sets the lowest temperature of the platform.
Remedy
Ideally, the glass platform could do with more nichrome wire which would improve the heat spread across the glass and reduce temperature differences between the heat element areas and non heat element areas. Unfortunately, adding more nichrome wire will mean buying a different rating wire to replace the wire already fitted and involve rewiring the circuit.
Before I start buying and replacing nichrome wire, I’m going to try changing the position of the thermistor to see if that will get me close enough to a better temperature controlled heated build platform.
Heated Build Platform Rework
The first attempt at modifying the heated build platform involved in moving the thermistor closer to the nichrome wire heating element. I secured the thermistor to the glass leaving a gap of around 2mm between the thermistor and the nichrome wire.
After returning the heated build platform to the 3d printer for testing, the results came as expected, the thermistor heated up too quickly causing the heater to turn off before enough heat could be transferred to the glass. The glass took too long to heat up from cold and could not reach the target temperature. The thermistor did not give a correct temperature reading from the glass because the thermistor was too close to the nichrome wire. The thermistor could not supply a consistent, stable reading around the target temperature. However, the heat is more evenly spread across the glass than before, which is what I’m looking for, but can only maintain a temperature at around 10 degrees C below target.
The second attempt was more successful, which involved in using a copper heat spreader attached between the thermistor and nichrome wire heating element. The heat was absorbed and transferred very quickly to the thermistor with a much improved short regular heating cycle. The target temperature was maintained with a stable reading from the thermistor and the reading matched that of the heat sensor gun when pointed at the glass area over the thermistor. The temperature difference across the glass build platform is a lot better than it was before which has been measured at around 6 degrees C just after the nichrome wire is powered off.
Conclusion
Changing the position of the thermistor worked really well, I now get an accurate stable reading from the thermistor and the temperature across the heated build platform is kept within the target temperature. This should be enough to stop the prints becoming unstuck through expansion and contraction of the heated build platform.
[bodyadsrich1l]